Crafting with metal isn't just about bending and cutting. It's an art of turning raw elements into functional masterpieces. With each bend, cut, and assembly, we don't just create products; we give life to your vision, adding value every step of the way.
Check Out All Of Our Services
For contractors seeking a swift and dependable partner, we're here to help you effortlessly achieve your contractual goals.
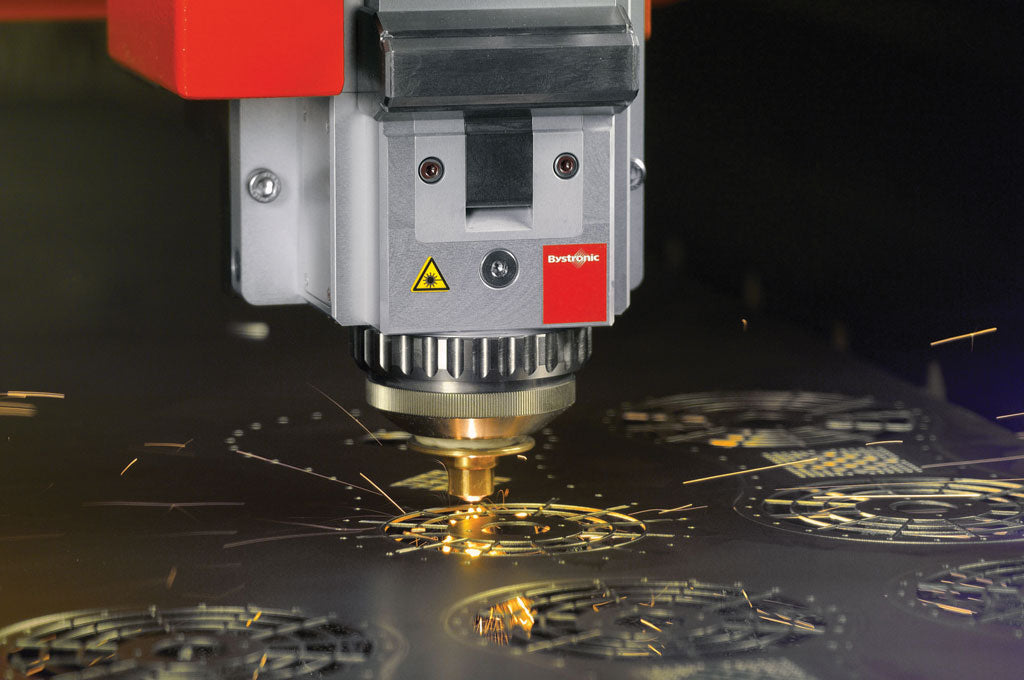
Sheet Metal Laser
Laser cutting is where precision meets artistry. Using a potent laser beam, we meticulously slice through sheet metal, whether it's stainless steel, steel, aluminum, brass, and copper. As the material melts and vaporizes, we're left with impeccably accurate cuts, ensuring minimal thermal disturbance. It's the perfect blend of versatility and precision.
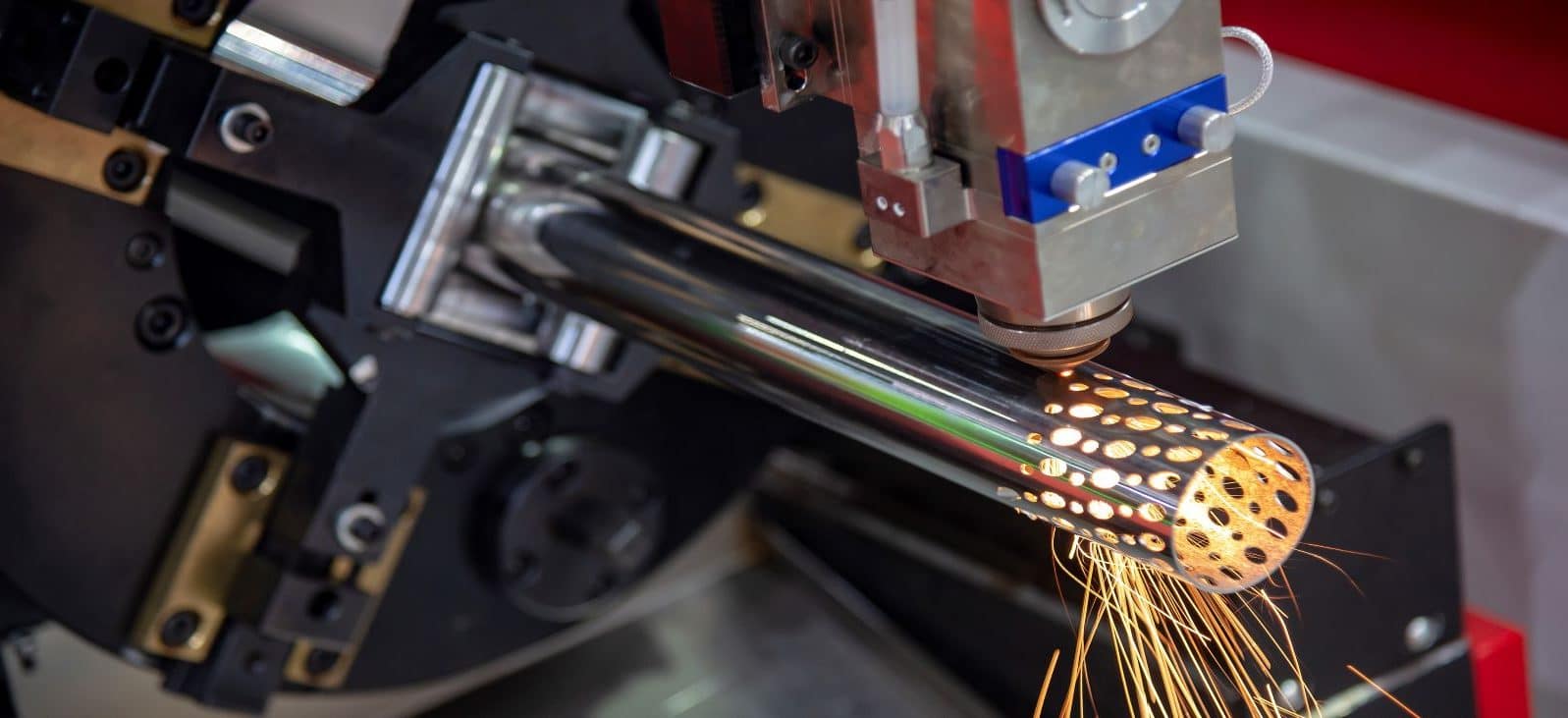
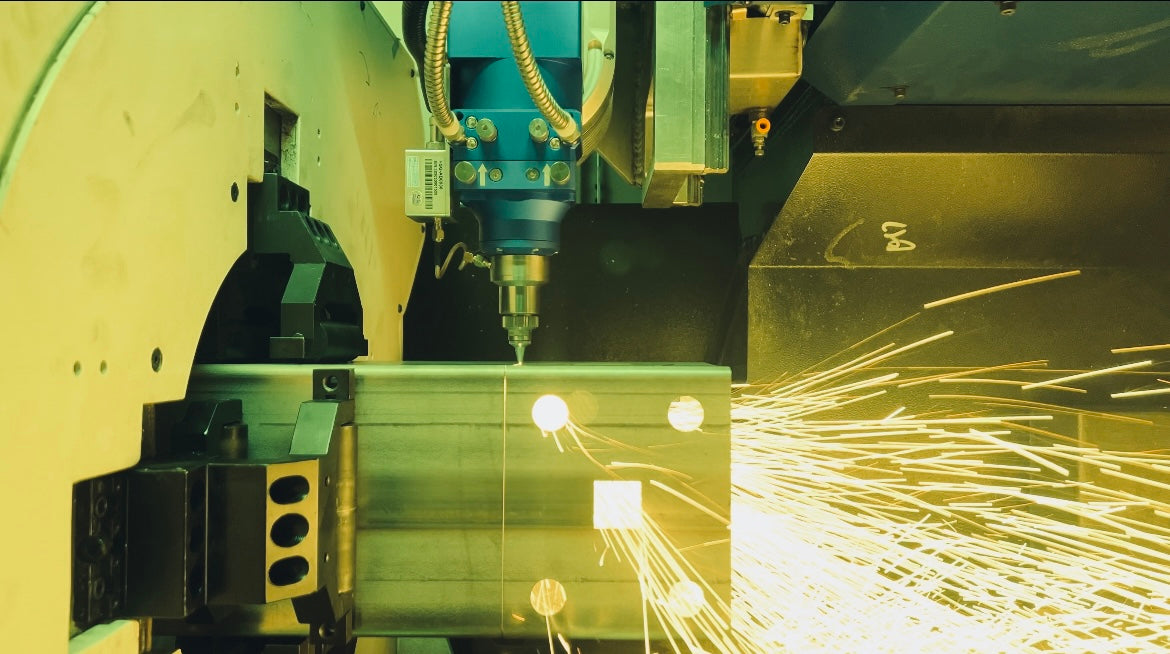
Tube Cutting
Tube cutting is an intricate procedure to attain the desired length or design of a tube. A spectrum of methods is employed depending on the specifics of the job:
Tube Laser Cutting: Embracing modern technology, laser cutting employs a laser beam to sever the tube. This technique shines when dealing with tubes with intricate designs or thin walls.
Band Sawing: Ideal for tubes with a larger diameter or robust walls, band sawing involves the use of a continuous band saw blade for cutting.
Abrasive Cutting: Suited for tubes with smaller diameters or slender walls, this technique employs a spinning abrasive wheel or disc to make the cut.
Cold Sawing: A method reserved for high-precision tasks, cold sawing utilizes a circular saw blade to achieve its purpose.
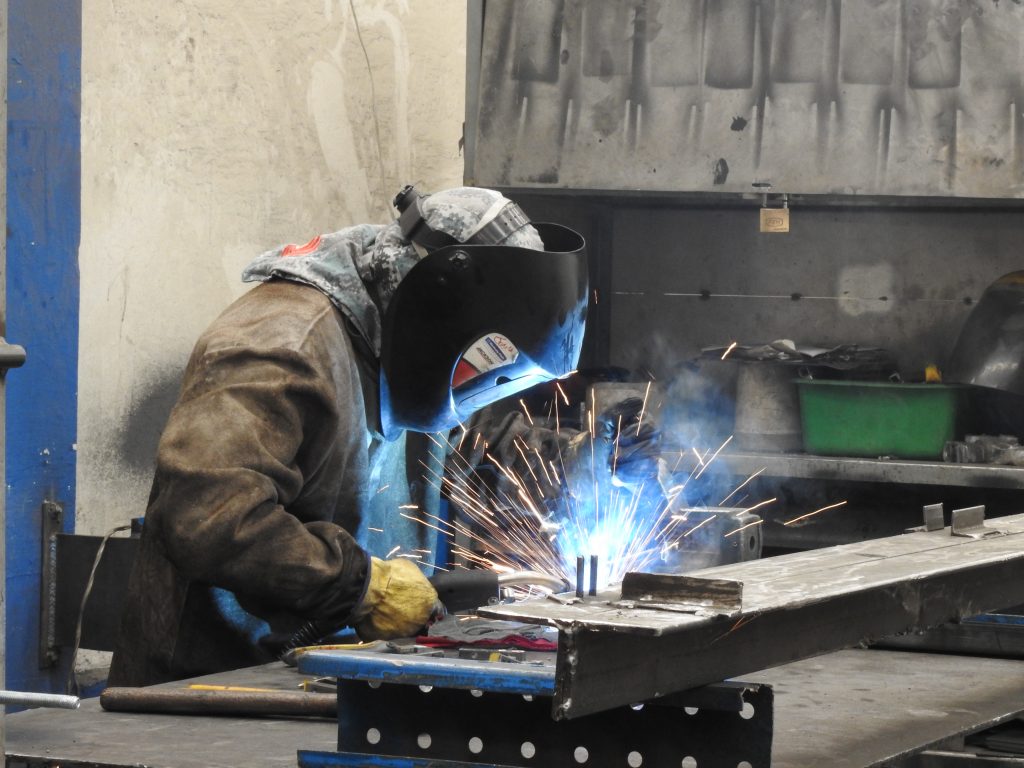
Welding
Welding is the art of fusion. With intense heat, we meld materials, predominantly metals or thermoplastics, turning separate pieces into one cohesive whole. Unlike brazing or soldering, which involve lower temperatures, welding ensures the base metal itself is seamlessly merged, providing unparalleled strength and integrity.
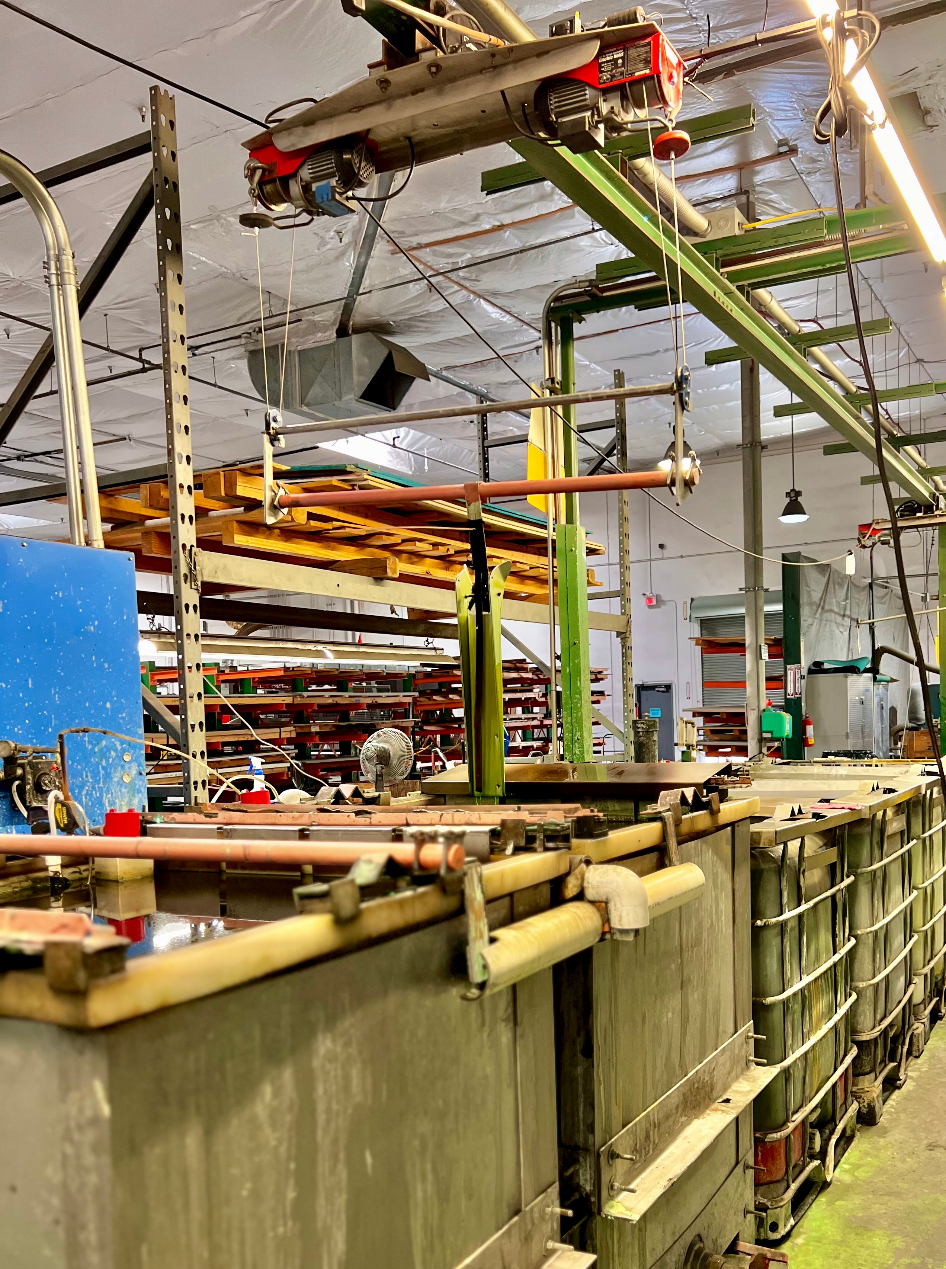
Electropolishing
Electropolishing is like giving metal a spa day. Through a refined electrochemical process, we delicately strip away a minuscule layer from metals like stainless steel, revealing a surface that's not just shiny and smooth, but immaculately pure.
Stainless Steel only, other materials, will contaminate our acid.
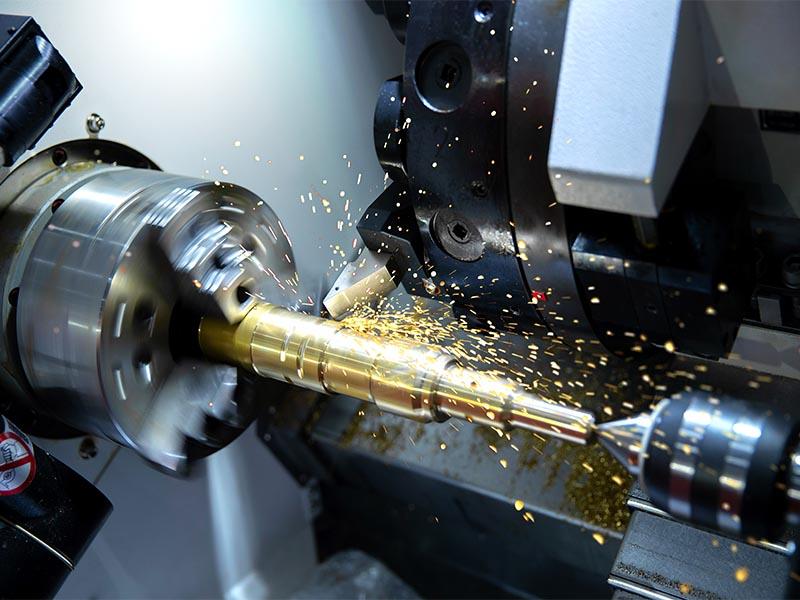
Lathe
A lathe is a vital machine tool used across multiple industries for its versatility and precision. By securely rotating a workpiece around a fixed axis, it allows a variety of operations to be performed, including cutting, sanding, knurling, drilling, and turning. The result is an object shaped with symmetry and accuracy. From shaping large components in the aerospace sector to crafting minute details in electronics and medical devices, lathes are indispensable. Additionally, many hobbyists and custom creators rely on lathes to bring their unique projects to life.
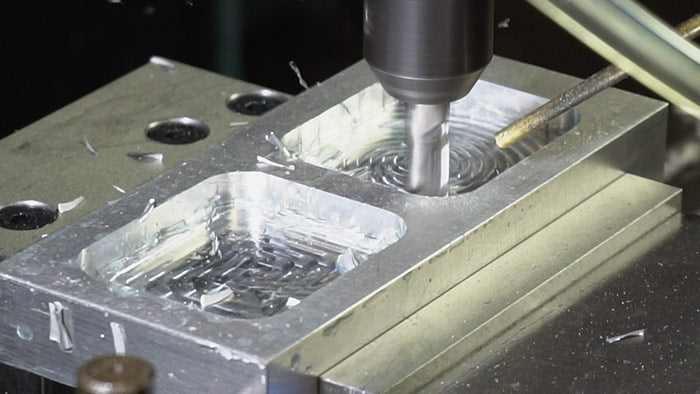
CNC Milling and Turning
CNC milling and turning epitomize precision in the world of computer-controlled machining.
Using CNC technology, complex designs are translated into digital directives, steering the machine's movements for unparalleled accuracy. In CNC milling, a rotating cutting tool methodically carves material from a securely fastened workpiece, navigating in three primary directions—X, Y, and Z. Made primarily of durable carbide or high-speed steel, these tools provide consistency, reducing errors and ensuring that the finished product perfectly fits its intended purpose.
The prowess of CNC milling and turning finds applications across various industries—from aerospace and automotive to electronics. These techniques guarantee precision-crafted components tailored for specific requirements, ensuring optimal performance in their respective domains.
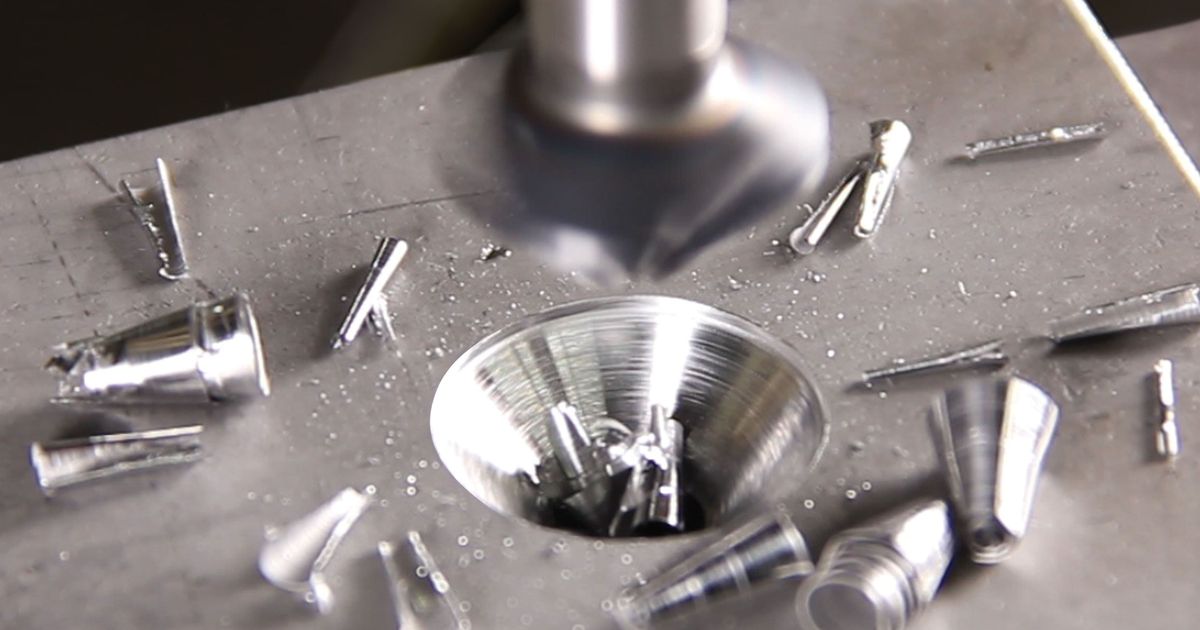
Drilling, Tapping, and Countersinking
Drilling: This process utilizes a rotating drill bit, often made from carbide or high-speed steel, to bore into materials. The drill bit, whether operated by a stationary drill press or a handheld drill, uses its spiraled edges to pierce the material, forming the desired hole.
Tapping: After drilling, tapping is employed. Here, a uniquely threaded tool, known as a tap, is used to carve internal threads within the drilled hole. This method allows bolts or other threaded parts to be seamlessly screwed in.
Countersinking: This technique creates a conical recess at the opening of a hole. Its primary function is to ensure that screw heads lie flush with the material's surface, resulting in a sleek and polished finish.
It's worth noting that while these operations may seem basic, mastering them demands a profound understanding of the appropriate tools and methods, ensuring precision and maintaining the material's quality.
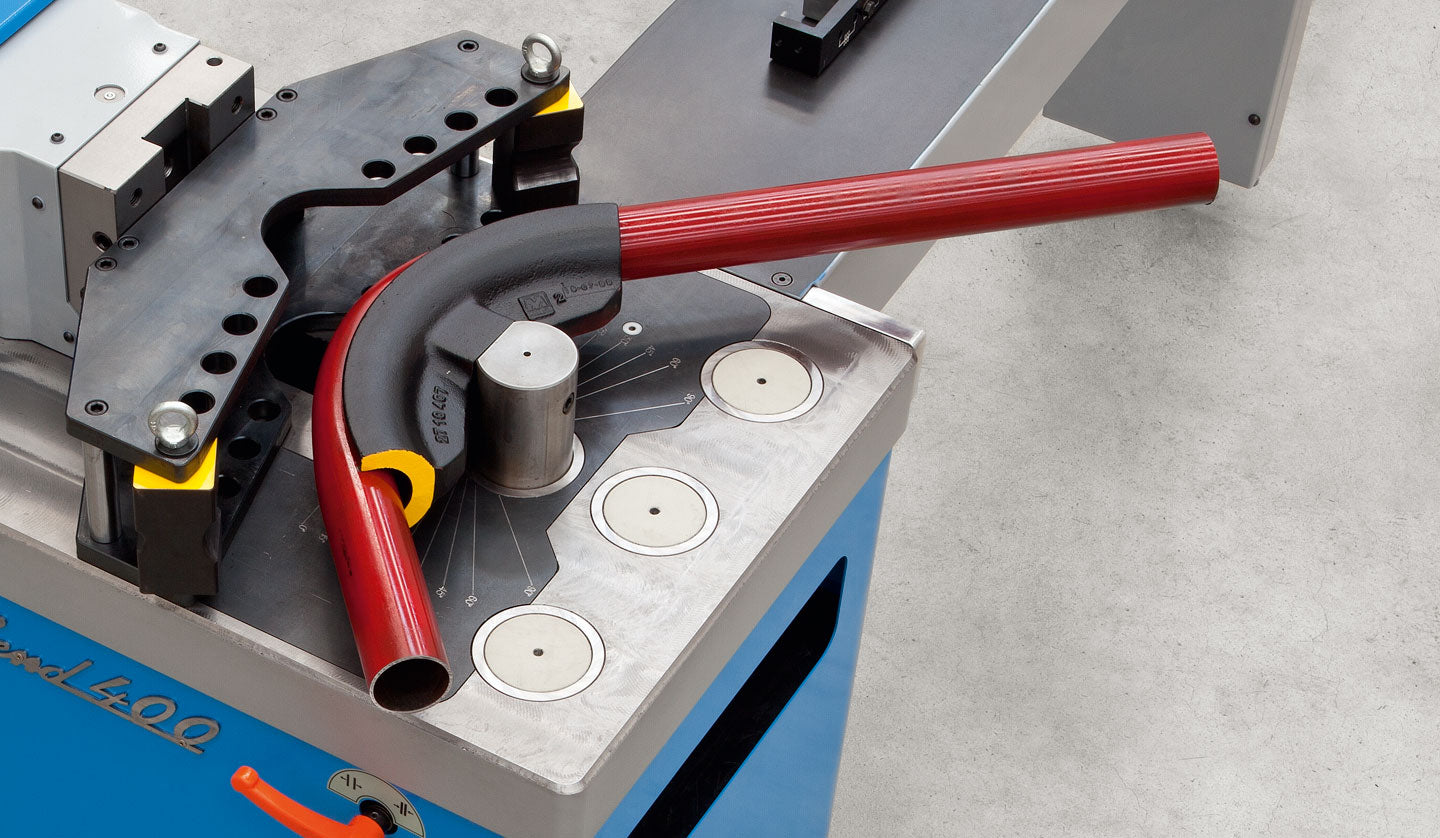
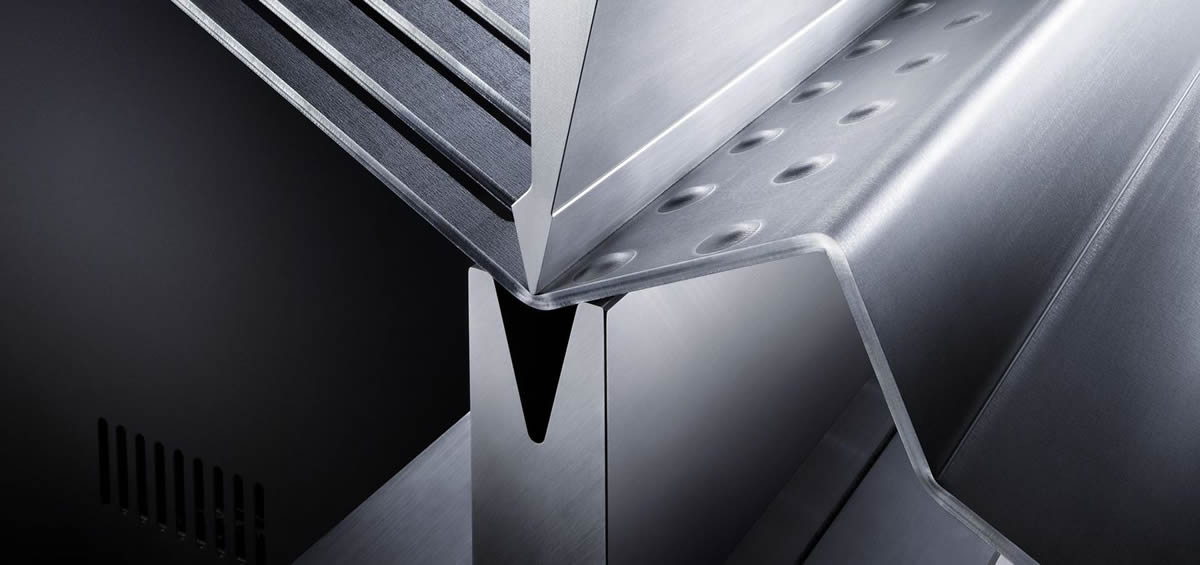
Sheet, Rod, and Tube Bending
Sheet Bending: This method revolves around morphing sheet metal into its intended configuration. The primary tool for this task is the press brake, a specialized device that exerts pressure on the metal, enabling it to assume diverse forms such as bends, angles, and channels. A gamut of items, from structural components to intricate designs, can emerge from this technique.
Rod Bending: Dealing with metal rods, this process strives to achieve a specific curvature or bend. A rod bender, designed to exert the right amount of force, is employed. With it, one can form various structures from the rods, be it loops, hooks, or even spirals. It's a pivotal technique, especially in sectors where precision in shape is paramount.
Tube Bending: As the name suggests, this is all about imparting the desired shape to metal tubes. A tube bender, an instrument applying targeted force, gets the job done. The outcomes? Shapes ranging from simple bends to more complex forms like elbows and tees, vital in a myriad of applications.
Despite the apparent simplicity of sheet, rod, and tube bending, mastery is essential. Utilizing the right instruments and adhering to best practices ensures not only the accuracy of the shape but also the integrity of the material in use.

Shot Peening
Shot peening is a cold working process utilized to fortify metal parts. By directing a stream of small spherical shot, typically crafted from materials such as metal, glass, or ceramic, onto the surface of a metal part, the method effectively bombards and modifies its exterior. The consequent dimpling effect generates compressive stresses within the part's surface. These compressive residual stresses confer several benefits, markedly enhancing the fatigue life, corrosion resistance, and wear resistance of the treated component. Thus, shot peening serves as a pivotal procedure for augmenting the durability and efficiency of metal components.
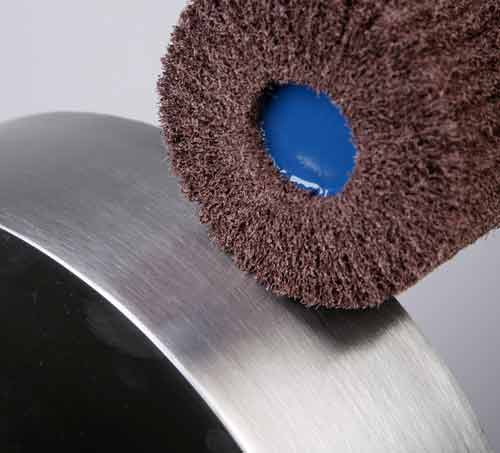
Graining and Satin Finish
Graining and satin finish represent distinct surface finishes implemented on metal, each offering a unique aesthetic and tactile experience.
Graining imparts a roughened, textured appeal to a metal part, achieved through several methods such as brushing, sanding, and blasting. This finish isn't just about aesthetics; it can also enhance the tactile grip on a metal component or be employed purely for its decorative impact.
In contrast, a satin finish bestows a metal part with a refined, matte visage. Achievable through techniques like polishing and brushing, the satin finish evokes a sense of quality and professionalism, making metal parts appear sleek and sophisticated.
Both these finishes are versatile in their applicability, suitable for a range of metals including stainless steel, aluminum, and brass. Their popularity extends across diverse sectors like aerospace, automotive, construction, electronics, and general manufacturing, highlighting their adaptability and the broad aesthetic preferences they cater to.
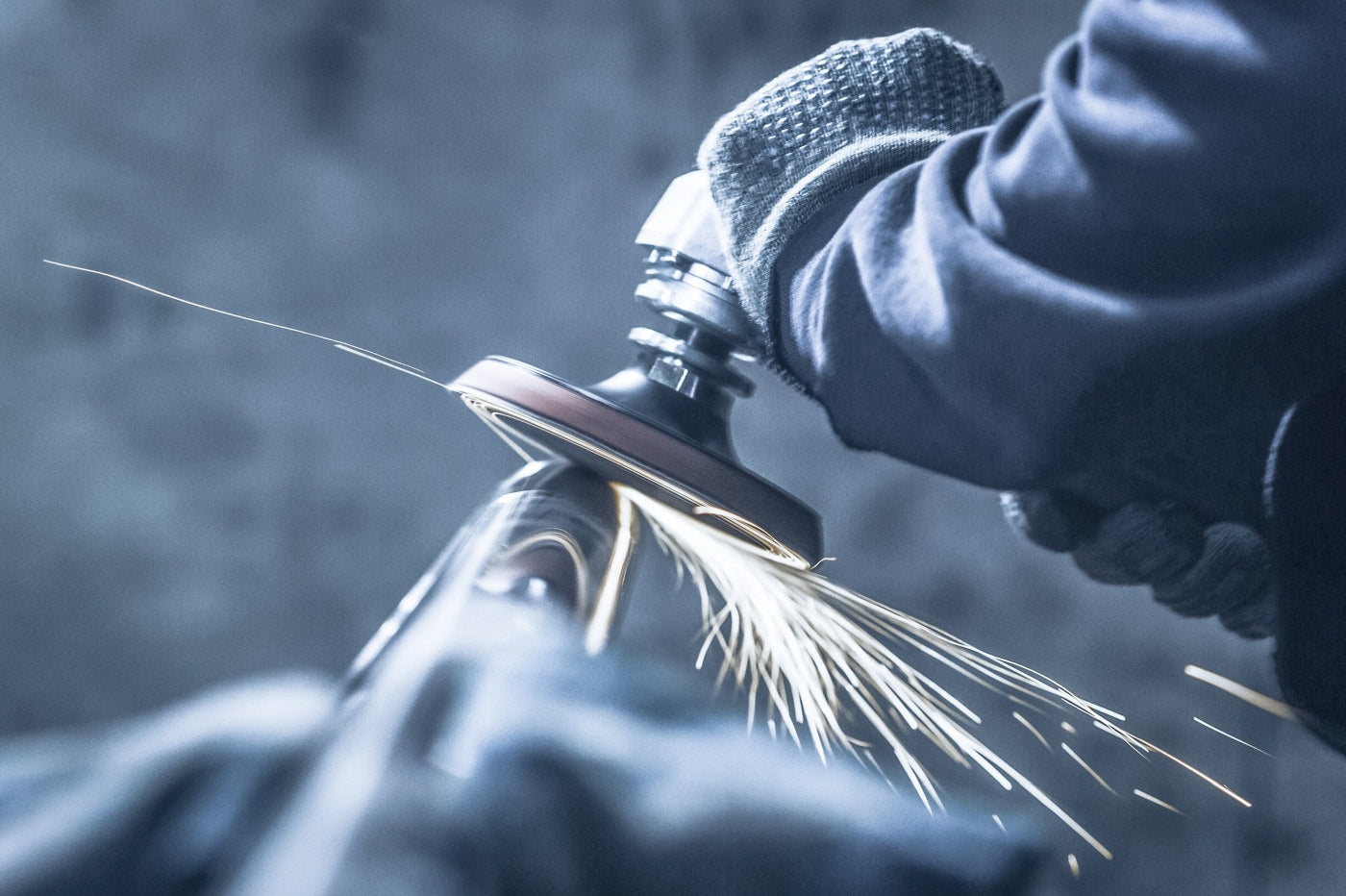
Buffing
Buffing stands as a vital metalworking technique that employs a spinning wheel or pad, in conjunction with an abrasive substance, to refine metal surfaces. The primary objective of this process is to eradicate blemishes, scratches, and any dull appearance, culminating in a lustrous, gleaming finish. Beyond mere aesthetics, buffing plays a crucial role in combating and removing signs of oxidation and corrosion, thus preserving the integrity and appearance of metal surfaces.
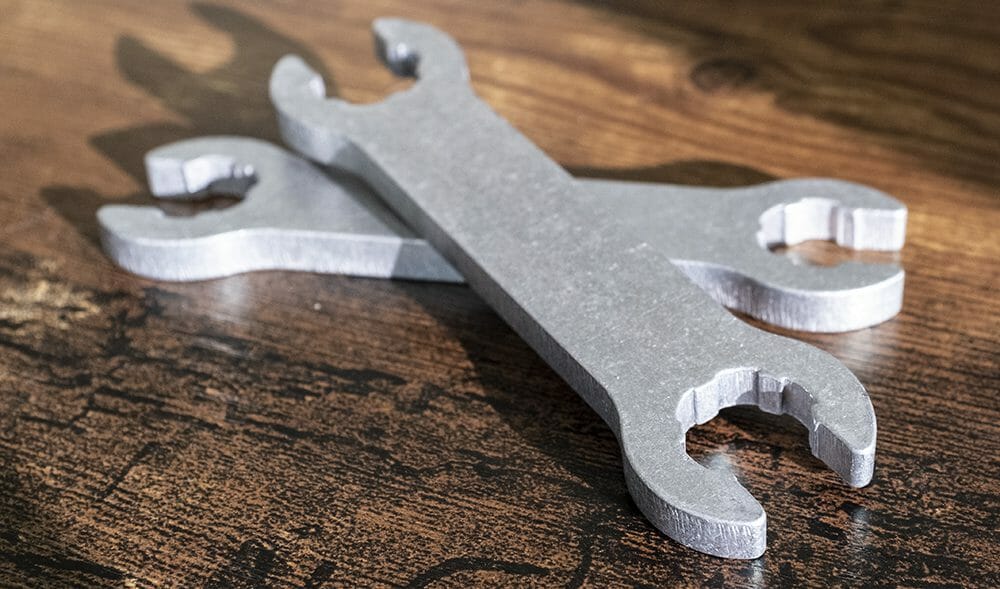
Tumbling
Tumbling is a metalworking technique that polishes metal parts using a rotating drum or barrel filled with abrasive media, water, and the parts themselves. As the barrel rotates, the abrasive media smoothens and polishes the metal, removing imperfections. This versatile process can yield various finishes, from matte to a high-gloss mirror finish.
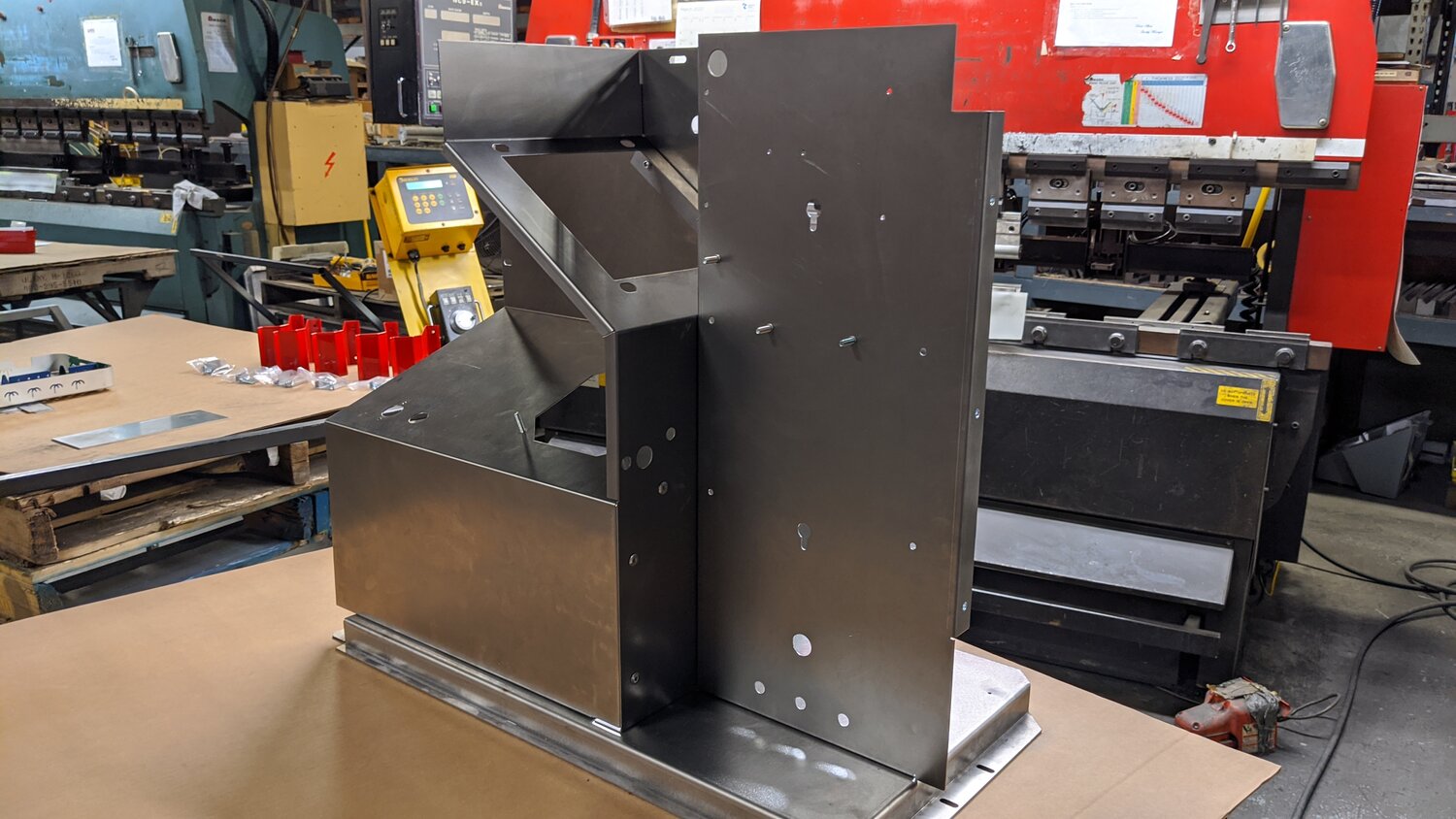
Assembly
Assembly involves combining multiple parts to construct a finished product. It's an essential phase in manufacturing, with the approach varying based on product intricacy and materials utilized. While manual assembly suits small-scale productions or items demanding precise attention, automated assembly is favored for mass production.